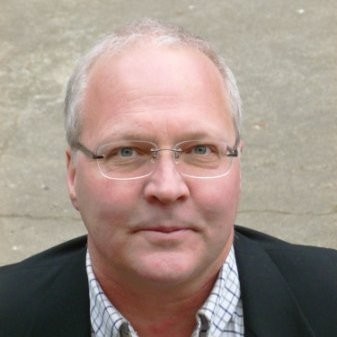
In 2010, Greg Howes co-founded CutMyTimber, a prefab mass timber company based out of Portland, Oregon, and he remains a partner at the company. CutMyTimber works with architects, structural engineers, builders and other fabricators, to supply custom mass timber products for a variety of building types, ranging from small cabins to 500,000 sf commercial buildings.
CutMyTimber has created products now used in hundreds of buildings in Europe, Canada and the U.S. They also fabricate green wooden buildings to the “passive house” and net zero energy standard and are currently developing their own line of mass timber ‘tiny houses’ as well as a new building system for both multi-family and commercial buildings. The company collaborates with the College of the Rockies, in British Columbia, to teach modern building systems, digital manufacturing, Cadwork (a virtual design software), and green building techniques to students in their Timber Framing program.
Greg is also a co-founder and board member of the AEC (Architecture, Engineering, Construction) Hackathon for developers and designers to collaborate and work with new automation, AI, robotics, etc. to look for solutions to daily problems in the built environment. Greg and his team have organized over 48 events globally to date. An AEC Hackathon will take place in Hangzhou, China, this coming December, and events scheduled for 2023 in Austin, Copenhagen, Dublin, San Francisco and Stavanger. He also organized “Mass Timber March Madness 2021,” a series of webinars that spanned a month, featuring speakers from around the world discussing mass timber production, general contracting, architecture, government, sustainable finance, and tech.
Read the podcast transcript here
Eve Picker: [00:00:07] Hi there. Thanks for joining me on Rethink Real Estate for Good. I’m Eve Picker and I’m on a mission to make real estate work for everyone. I love real estate. Real estate makes places good or bad, rich or poor, beautiful or not. In this show, I’m interviewing the disruptors, those creative thinkers and doers that are shrugging off the status quo in order to build better for everyone. And speaking of building better, I’m very excited to share that my company, Small Change, is now raising capital through a community round that is open to the public. Small Change is a leading equity crowdfunding platform for impact investment in real estate. For as little as $250, anyone 18 and over can invest in Small Change, helping to fuel our growth as we disrupt the old boys club of capital that routinely ignores so many qualified people and projects. Please visit Wefunder.com/smallchange to review the full details of our raise and to make an investment if you can. And remember, investing is risky. Don’t invest more than you can afford to lose.
Eve: [00:01:46] My guest today is Greg Howes, co-founder of Cut My Timber. Cut My Timber is a fabricator of timber and steel components for the entire building industry. Their projects are spread as far as Alaska, Quebec and Australia, with production based in Portland, Oregon, and an office in Vancouver. They are able to make highly complex and efficient building systems available to both large and small companies, as well as to individual independent builders. Cut My timber uses state of the art computer software to optimize projects. This optimization results in less waste and offcuts, so they can build greener at lower cost. And now they are pushing their technology even further, building to passive house and net zero energy standards. Finally, let’s not forget the mass timber tiny homes they are developing. Listen in to hear more. If you’d like to join me in my quest to rethink real estate, there are two simple things you can do, share this podcast and go to rethinkrealestateforgood.co, where you can subscribe to be the first to hear about my podcasts, blog posts and other goodies.
Eve: [00:03:13] Hi Greg, Thanks so much for joining me today.
Greg Howes: [00:03:16] Good morning.
Eve: [00:03:16] So, you’re really heavily involved in the mass timber industry. Can we just back up a little bit and you tell me what mass timber is for people who don’t know?
Greg: [00:03:29] Yeah, I think it’s not really come on the radar in the US, except over the last ten years. And then very slowly, it’s been a real niche market. Essentially, I think a different way to think about it as heavy timber as opposed to two by fours and two by sixes. It involves glulam beams and also now increasingly what’s called cross laminated timber or nail laminated timber. And a simple way to think of that as really thick plywood. But you’re essentially making it out of often two by sixes and you’re stacking them, a layer of them, and then you make another perpendicular layer and glue those together, then typically do a third or more layers. So, you have it almost like a very thick sandwich of lumber and it comes in very, very big panels. I mean, you know, even larger than like ten by 30 or 40 feet. And that’s a single panel. It’s very strong. It’s obviously very thick. And that is used in many ways for walls, typically, floors, roofs, ceilings with it in buildings and mass timber in my research was actually, I mean, cross laminated timber itself was invented almost a hundred years ago actually in Tacoma, Washington.
Greg: [00:04:48] But it really took off in Switzerland and Austria in the nineties and they’ve been doing a lot of buildings with it. Initially, it started as a way to use less strong wood, not even almost waste wood, but it was a way to take wood that wasn’t structurally as strong and essentially through engineering and making this bigger, gluing it together and using automation to manufacture it has more engineering strength. And what’s happening now is that has come into the US market where again, following the Switzerland, Germany and Austria in doing this, and it’s really booming. And when I think of its most attractive properties are, one that it quite literally it’s very difficult, it doesn’t burn. It does burn, but it’s like having a campfire and trying to start the campfire. Not with twigs, but big logs. The outer layer, when it does burn, it’s really hard.
Eve: [00:05:43] I do that all the time.
Greg: [00:05:45] Yeah.
Eve: [00:05:47] A lot of smoke. Goes out quickly.
Greg: [00:05:50] Well, it does. And then it creates that char layer on the outside. So, even if you have that big log and you throw it on the fire and you leave it on all night, even on a big raging fire, it generally won’t burn through because it will have that char layer on the outside. So, it has some really good properties for fire and again, it can be very, very strong. And another big advantage is you can construct the buildings very rapidly, because essentially you’re building digitally before you build on site and you’re essentially manufacturing and custom cutting all of the pieces. So, let’s say the cross laminated timber and all the beams and all the connectors, you’re essentially doing that work before the trucks go to the job site and assemble the building. And when you do that, well, it can be really, really efficient. I give it many examples where buildings are literally going up in a matter of days, and this includes buildings of many stories, including ones we’ve been involved in. You’re doing a five-story building. The foundation is in all of the concrete and then you come in with the trucks and essentially you have a crane, and everything gets assembled extremely rapidly. And then the building continues with all of the things that go inside the building afterward. I think it’s a big advantage.
Eve: [00:07:04] So, what’s the primary problem that we’re trying to solve with mass timber?
Greg: [00:07:08] Well, big not only with mass timber, but in construction in general. We don’t have enough buildings where we’re short of builders and also, we want to build more sustainably. I think there’s a growing interest internationally. I’m obviously in my niche market, so I view the world from the mass timber perspective, but we need a lot more buildings and we need to figure out how to build them more sustainably. As we know, concrete is responsible I think for 8% of the global carbon production, just through making concrete. And so, we need to use more environmentally friendly materials. We need to figure out how to build faster, smarter, less expensive. And we have to do that in a world where we don’t have enough to be blunt builders. And so, how are we going to do that? So, I think creating building systems is one of the best answers. And specifically with cross laminated timber, you can build much higher. There are buildings, I think the biggest one in the world now is in Milwaukee, The Ascent building.
Eve: [00:08:15] Yeah, I just read about that. Yeah, yeah.
Greg: [00:08:18] I think it’s 26 stories, and there are buildings much, much taller that will be made primarily from mass timber. So, there’s a boom in, let’s call it timber skyscrapers. But I think every building is actually a hybrid of materials, so it does have concrete in it and wood and metals, just to different ratios. The big problem I think we’re trying to solve also as well. How do we take Woods and make them stronger through engineering processes or through the factory? How do we do more with wood? And use it more efficiently. And what I think the mass timber boom has created is a way to build taller with wood. And because when you build this way, unlike conventional building, and I’ve been a builder for 25 years, you can go to Home Depot and order a lot of two by fours and then try to figure out how to build your house on the job site. With mass timber, that’s not really realistic, simply because the beams and the laminated timber products are too big. You can’t really cut them precisely on the job site. So, you have to do that work in a factory. Yeah.
Eve: [00:09:33] Yeah. So, basically, it’s like ordering a steel member or a cross line beam ahead of time and making sure it’s sized correctly. Like we’ve been actually doing that for years, right? But now it’s shifting to it sounds like many more elements in the building.
Greg: [00:09:49] Yeah, we’ve been doing it for years. If you drive by and you see a steel building, generally all of those parts or the majority of them are pre-cut and predrilled and the builders job is essentially to assemble those and figure out how to do that efficiently. And we’re applying the same thinking to mass timber specifically.
Eve: [00:10:09] How does this help forests? How are we going to save our forests if everyone’s going to be using timber buildings?
Greg: [00:10:15] I am not a forestry expert. There are many people who are. I defer to them. We do use wood. Here’s my question, the wood we do use, we should do more with it. We should use it efficiently and we should use lumber that comes from forests that are well managed. They’re sustainably managed. In the US, there are a lot of statistics, we’re actually adding to our supply of forestry. We’re having more forests that we can harvest. And the US is the biggest country in the world to build with wood. About 93% of Americans lived in a wood framed home. So, my answer to that is like, well, let’s use the resource that is sustainable and renewable. Let’s use specifically wood that is from a sustainably managed forest. If we use good building systems, we can reduce the amount of wasted wood, a lot. We can quite literally have only a couple percentage points of waste as opposed to conventional construction. That, as you know, creates a lot of the waste.
Eve: [00:11:23] A lot of waste, yeah.
Greg: [00:11:24] Well, I think we can build buildings that use wood, use it more efficiently. We can do more with that wood because we’re creating things like glulam beams and cross laminated timber, and we’re figuring out how to do that efficiently. And we can use the forest the same way we build better and more sustainably with them.
Eve: [00:11:46] What percentage of buildings being built today use mass timber, and how do you think that might change over the next five or ten years?
Greg: [00:11:54] Oh, of all the wood buildings in the US, the percentage that use mass timber is far less than 1%.
Eve: [00:12:01] Oh, it’s tiny.
Greg: [00:12:02] It is a tiny niche market, it is growing. There’s quite a few people in the industry that think the US will become the largest market in the world for mass timber buildings in a short number of years. The same way the US already is the world’s largest market for wood frame buildings in general. But because mass timber is very good for specific kinds of buildings, it’s highly likely that we’re going to become the biggest market of all.
Eve: [00:12:30] And how quickly is that going to happen, do you think?
Greg: [00:12:32] It’s not a demand problem. I think you read the same things I do. We’re short of houses at every price point in many parts of the country. So, we don’t have enough buildings. We have people who need them. It’s difficult to build. I think the growth of building systems where you’re essentially already, call it prefab, buildings is going to grow because it’s really one of the only solutions. We’re suddenly not going to have a lot more carpenters. And it’s the same reason I got into this. It’s like, how do I build more buildings? How do I deliver more complexity? And I think the answer is through building systems. Mass timber is booming, where our factories based in Oregon, Oregon produces the most softwood lumber of any state. There’s a lot of demand out here. Most buildings are, in fact, wooden buildings, and where mass timber is the best product for that type of building, there’s a lot of demand. It’s actually growing faster than the supply. And I would argue that the shortage is of factories that do create the kit of parts for mass timber buildings. There’s not enough of those, and it takes years to build them. And they’re expensive. They’re full of very expensive machines.
Eve: [00:13:53] The actual factory, yeah.
Greg: [00:13:56] There’s interest in mass timber and I think it’s growing, and there’s more interest than there are available supply, and the supply comes through those factories and there aren’t very many of them. That’s the constraint to its growth.
Eve: [00:14:10] So, are you seeing people investing in factories like that? Like are people beginning to understand that issue?
Greg: [00:14:19] Well, there are investors coming in. I’ll give an example. In Europe, Stora ENSO is a Swedish Finnish company. They keep building factories, they’re one of the biggest producers of cross laminated timber in the world. They continue to build more factories and demand exceeds supply in Europe as well. We are having some factories come into the Canadian and US market. One of the biggest suppliers in the world that’s new is a company called Sterling, based in Chicago. Their product just became certified as a cross laminated timber panel, and it’s certified in that it’s legal to use for buildings. So, they’re one of the world’s biggest producers now. So, we’re seeing more companies invest in Canada and in the US. I know them, it’s still a niche market. But the constraint, the bottleneck right now is, well, we’re going to have we have a lot of lumber, we’re going to have more mass timber product, but we need those factories that create those custom kit of parts. That’s what we’re short of. That’s the big bottleneck.
Eve: [00:15:26] That’s interesting. And other than that, is there any specific work that needs to be done to advance mass timber? I mean, you talked about the fire resistance of these really heavy pieces of engineered lumber, right?
Greg: [00:15:39] Correct.
Eve: [00:15:40] Does the building code recognize that? What needs to be done to advance the idea?
Greg: [00:15:45] A lot of work needs to be done on many fronts. And I want to clarify, I am not a forestry expert. I am not a fire expert. I’m not a structural engineer. There are lots of great organizations, people doing the research and also the building codes are being changed and updated to allow for these tall buildings in more municipalities. A big challenge we have in the US, as you know, building codes vary a lot.
Eve: [00:16:17] They do.
Greg: [00:16:18] Based on the municipalities. And not only do the building codes vary, the fear among the local building code officials, but also among the builders. You have a lot of builders, architects and structural engineers, and they hear about this mass timber thing, but they haven’t worked with it before. And there’s a lot of perceived risk in using a new product or a new process. And so, the good thing is there’s a lot of research being done for those interested in fire and structural engineering. I would point people often to research that’s being supported by the US Forest Service and others. It’s happening at a lot of universities.
Eve: [00:16:57] Yeah, it’s really interesting. So, it’s really early days. It’s pioneering efforts still. But you know, I’ve also heard people say that there’s a mass timber boom on the way. Is that, do you think that’s true? Is that going to take a while to ramp up? It sounds like there’s a number of issues to resolve first.
Greg: [00:17:13] Again, since I’m in the industry and have been for decades, my perspective is very biased. I think a lot more people are hearing about it if they’re paying attention at all to what’s happening in the world of construction and specifically with wood, I would say there’s definitely a boom happening, certainly across Europe, Australia, New Zealand and in Canada and the US. When I speak to people in the industry, it’s very much boom times. And the biggest conference that happens in the US is the Mass timber conference in Portland, Oregon. About every March a few thousand people attend and when we were there last year, everyone’s like talking about how it’s extreme boom times. There’s essentially too much work and not enough supply.
Eve: [00:17:59] Interesting. And who’s at the forefront of the mass timber movement in the US?
Greg: [00:18:03] Oh, that question is similar to asking who’s at the forefront of construction in the US. It needs to be much more nuanced.
Eve: [00:18:13] Well, nuance it for me. Okay.
Greg: [00:18:19] I think what it is, when working with mass timber and to be able to do it well literally requires some experience. Because it’s a different process. It’s not designing a building and here’s a ten-story building, should we build it out of concrete, steel or mass timber? And then say, well, who’s the lowest bidder? We’ll build it that way. That literally doesn’t work. The architects are learning how to work design for mass timber. How does it work well, and when is it the right product? The same goes for the structural engineers. If you haven’t worked with mass timber buildings before, there’s a tendency to over engineer. And over engineering makes buildings more expensive and take longer.
Greg: [00:19:04] And builders, as a builder myself, and I’ve been one for 25 years, if you haven’t worked with mass timber before, the question becomes, well, how do I price that out? What is it going to cost me? And too often in construction, your big cost are your materials and your labor. But if you do mass timber efficiently, much of the labor is moved into the factory for the mass timber frame because you’re figuring that out, you’re shipping it to the project. It’s hard to know how to price that if you’re a general contractor who’s never worked with mass timber or prefab before. There are quite a number of people in each of those categories, architects, structural engineers, builders, subcontractors. And these factories that produce the kit of parts. There’s a small number of each of those who have experience, but there’s nearly exponential growth on the total number of mass timber buildings. We’re lucky that we’re out in Oregon. Oregon produces so much wood. The state’s been very supportive of mass timber and the US West Coast, California, Oregon and Washington. That makes up about 50% of the total market for mass timber currently. Canada is doing a lot as well.
Eve: [00:20:16] That makes sense. You know, I can understand why it’s been ahead in places like Finland and Sweden, the very northern Europe, where it’s very long, cold winters. So, this manufacturing system would permit you to be building, you know, when you really can’t work outside, right?
Greg: [00:20:32] Correct.
Eve: [00:20:32] Or not very comfortably. So, is that true too? Do you think northern states are taking onto this idea faster than southern states in the US? Or don’t you see that differential?
Greg: [00:20:43] I’ll touch on the Nordic Scandinavian countries. Europe is so different than the US because let’s say this, over 80% of the buildings in Europe as a general rule of thumb, are made from concrete. That’s essentially the primary building material. The more you go north, let’s say, to Sweden, the more wood there is, the more it’s used in construction. And even in Sweden, I like to tell people prefab, single family housing is the norm. Prefab for your housing, that reached 50% market share in the 1950s. So, this whole idea of prefab and prefab using wood is quite common in Germany, Switzerland and Austria. But it’s still like 10% of the buildings in Scandinavia, it’s much more. How will that come into the US? I think it will, not only here on the West Coast, will it be very common. It will become more common in Georgia and Alabama. They have a lot of loblolly pine there and there’s a lot of it. Some would argue there’s almost too much of it. And so, there are some new factories coming in to the southeast of the United States that will begin to produce more and more mass timber, very cost effectively. So, that supply will ramp up a lot. But again, the bottleneck will still be those factories that take those commodity wood products and make them into buildings.
Eve: [00:22:06] So just changing gears a little bit, I’m just wondering a little bit about your background. How did you get involved in mass timber?
Greg: [00:22:13] I’ve been a builder of homes for most of my life. I’ve also worked in tech, and had startups, and worked in other countries and other industries for short periods of time. But the majority of my work has been in building. Over 20 years ago after I had a startup in Silicon Valley, and we had the whole crash in Silicon Valley, again around that was exactly when we started our company. So, our timing was bad. So, we had a company not related to housing, that shut down. And I said, look, I’m going to go back to building, but if I’m going to go back to construction, I want to do it efficiently. I want to figure out the best way to build. And so, I toured many factories in Canada, the US and Europe, and said, I want to build with wood on the West Coast. How do I do that efficiently? Because life is too short to become an architect, engineer, builder and everything else all at once. I need to use a system and I want to use the best system for building with wood. So, I did tour all of those factories and I recognize it’s a question of software and it’s a question of systems. And that’s when I encountered mass timber. And so, I specifically focused in on that and ask, well, who’s doing that really, really well? And 20 years ago in the US, almost no one was.
Greg: [00:23:44] So, the leaders were in Europe. So, then my research led to, well, what are we learning from the Europeans and how do we apply that here? And then I found the person who’s now my business partner, Stefan Schneider. He was a Swiss immigrant. He’s been here for 20 years, and his job for six years was setting up factories. He was the person you called when he wanted to enter the industry.
Eve: [00:24:07] Interesting.
Greg: [00:24:08] And I said, well, look, I really want to build with wood. You’re the person who’s the most knowledgeable in my experience. Why don’t you start your own factory? For the last six years, you’ve been setting up other people’s factories across Canada and the US. Why don’t you come to Oregon and start your own factory, which he did. So, we’ve been, since 2010, we’ve had a factory in Oregon and we’ve been fabricating mass timber components, kit of parts, on literally hundreds of buildings. And then I want to emphasize, in doing so, we are one of a team of companies that do mass timber buildings. So, we have a pretty big network of architects, engineers, subcontractors, assemblers, many other people. Right?
Eve: [00:24:54] Your company’s got a great name. Cut my timber. I really like that. So, what sort of projects have you built and what does it look like? Do architects come to you or clients or all of the above or engineers? Like, how do you work?
Greg: [00:25:08] All of the above. There is no single mass timber marketplace. Let’s use an example. Let’s say Eve Picker wanted to do either a ten-story mass timber building or you wanted to do ten single family homes using mass timber. And you ask yourself, well, where do I go to do this? Who does this? Who does it well? There isn’t a single place on the web where you can go to find that information. And many of the companies that actually do it are booked out for years, or at least for a very long time. So, they’re like, well, look, it’s great you’re interested in a project, but we don’t have capacity. That’s kind of a problem that may change because more stuff’s coming on the web. But again, there’s no central hub. What happens to us?
Greg: [00:25:51] We’ve been in the industry long enough that we get approached generally through company and people we already know, and they are architects, general contractors, general engineers, some real estate developers. They’re interested in mass timber, and they ask around and find out, well, who does this, who has experience doing this? And they come to us and sometimes we play a big role in the project and other times we’re a subcontractor supplying a small part. I’ll give you an example. There’s an extension of the Portland Airport in Portland, Oregon. That project is over $1,000,000,000. We are one of hundreds of companies supplying that project, so we do some wood fabrication. On other projects, we’ll do a single-family home, let’s say a timber frame or glulam home, we’re the major supplier. We do commercial buildings. We supplied big beams to the new Adidas headquarters in Portland, Oregon. That’s over 400,000 square feet. And then we’ll do event structures like the one in the background behind me.
Eve: [00:26:58] Which is amazing.
Greg: [00:26:59] If you’ve ever watched a TEDx talk, we created the stage for the TEDx talk. That’s 12,000 individual pieces of wood specifically, mostly glulam. And that was all modeled and then fabricated and shipped up as a kit of parts. And that’s a good example of another mass timber project.
Eve: [00:27:18] That’s a really big range. Yeah. So, how do everyday people get into this market. If I just wanted an affordable home, but I really care about the environment and I want to find someone to help me build a timber home, the entire home.
Greg: [00:27:36] There are multiple ways to go about that. There are some for a single-family home. And again, with mass timber, let’s use some examples of a… There’s the homes constructed with essentially two by fours, two by six is in small beams. On the heavy or mass timber side of things, there are homes that are, let’s say, using a lot of glulam beams. Um, there are timber frames. Those are solid wood not engineered wood, it’s just solid pieces of wood. And then there are many homes that are a hybrid. They may be heavy beams and CYP panels, structural insulated panels. So, there are a growing number of suppliers who try to be a one stop shop. That you’ll go to them, and you can buy the home you want from their kit of parts, from their catalogue, or you can have a custom home designed and manufactured and built for you. In this big country, there are many options.
Eve: [00:28:35] There are many, many options. Yeah.
Greg: [00:28:38] And the price points are very varied as well, too. Some companies will focus on accessory dwelling units for your backyard. Other companies are doing big custom homes in ski resorts. It’s very varied.
Eve: [00:28:51] Right. So, I’ve heard whispers from you that you also want to manufacture houses. You want to talk about that, as a way to really produce housing quickly?
Greg: [00:29:03] Yeah. Our company and others, we think a way we can scale and become more efficient and make the whole system better is essentially through developing a catalog of buildings and a building system. Right now, everything, as you said, is bespoke. We have one project like the one behind us and then the next one we’re doing, working on an airport, or we’re working on a large commercial building. That works, we’re very busy doing that, but it requires very different skill sets. And we work with billion-dollar construction companies and the next time we’re working with a general contractor with five employees. So, we have a good business doing that. But we think the way forward, we want to use some of our capacity and we’re developing a line of single-family homes. And so, we’ll sell those as a kit of parts to other builders and to, let’s call it the do-it-yourself crowd, that they do want a mass timber, or a heavy timber home and they want it as a kit of parts. So, we are developing that. We don’t have it ready yet, but we are developing that, and we are building a new factory. Our current one is in Portland, Oregon. We’re building another one that will open up in the first half of next year outside of Portland, and we want to use some of our capacity to do that, that catalog of single-family homes. And we will, and we’ll have that ready in late spring.
Eve: [00:30:39] It feels a little retro, like going back to build your own log cabin, right?
Greg: [00:30:43] It is, But the housing demand is so extreme. So, I think the solution to creating more housing is there are millions of solutions. There have to be many ways. Some people want a big house, some people want a small house. Some people want a net zero home. So, we want to be one of the many providers of solutions.
Eve: [00:31:02] Well, it’s really interesting. So, final question for you. Are there any other current trends in mass timber that we should keep an eye on, like new products emerging?
Greg: [00:31:11] Here’s what I think you should look, when you look at mass timber. Think of, there’s cross laminated timber that’s glued together. There’s also nail laminated timber where the layers are connected with nails and then there’s double laminated timber. So, go into the whole category, understand that there are many kinds of heavy or mass timber. An exciting trend, there’s growing interest in net zero building. There’s growing interest in Passive House. So, the combination of mass timber being fabricated in a factory and they’re addressing the market of green building and specifically net zero and sustainability, where those trends are converging. Is there a way to build in a factory smarter, greener, more sustainable homes for the people who want them? And will these building systems make them more affordable? That’s what excites us, and I think those are all growing trends.
Eve: [00:32:08] Yeah, I agree with you. They’re definitely growing. Well, this is really exciting. I hope you stay in touch and let us know when your factory opens. I want you to send me the catalog.
Greg: [00:32:18] I will. And here’s a real convergence that I think aligns with all the innovative work you’re doing in crowdfunding. I do want to see crowdfunding merge with mass timber and prefab. So, people who want a home or they want a community are finding one another through crowdfunding and they’re working with the factories that can actually produce the buildings either as an investment or for the home they want. That excites me as well.
Eve: [00:32:50] Yes. It would be a lovely world, wouldn’t it?
Greg: [00:32:54] Well, we’ve got to make it happen.
Greg: [00:32:56] Yeah. Well, thank you very much for joining me. And I do expect to get that catalogue when it’s ready.
Greg: [00:33:02] You will.
Eve: [00:33:02] I can’t wait to see it. It sounds like a lot of fun.
Greg: [00:33:05] In late spring next year. I’ll share that with you.
Eve: [00:33:09] Thank you.
Greg: [00:33:09] Thank you.
Eve: [00:33:17] I hope you enjoyed today’s guest and our deep dive. You can find out more about this episode or others you might have missed on the show notes page at RethinkRealEstateforGood.co. There’s lots to listen to there. You can support this podcast by sharing it with others, posting about it on social media or leaving a rating and review. To catch all the latest from me you can follow me on LinkedIn. Even better, if you’re ready to dabble in some impact investing yourself head on over to wefunder.com/smallchange, where you can invest directly in Small Change and our mission to democratize capital formation to create impact in commercial real estate development. A special thanks to David Allardice for his excellent editing of this podcast and original music, and a big thanks to you for spending your time with me today. We’ll talk again soon. But for now, this is Eve Picker signing off to go make some change.
Image courtesy of Greg Howes