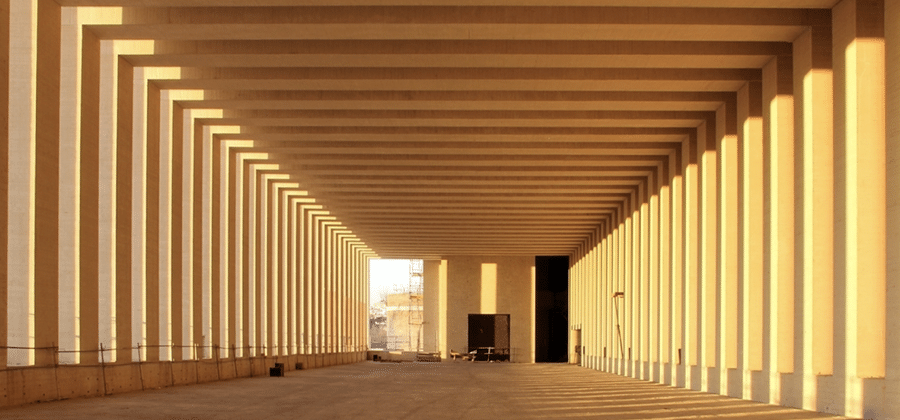
Mass timber is a catch-all name for a range of engineered wood products. Smaller, non-structural pieces of wood are glued together and engineered in such a way that together they become much larger and structural elements. Mass timber has many attributes. Speed of construction is a major benefit. Panels are pre-manufactured and pre-cut before delivery. These panels can be fitted and screwed into place by a small crew. An entire floor of a large building might be made up of only five or six panels. And an 8-storey building might be constructed in as little as two weeks.
A familiar mass timber product is Glued Laminated Timber (glulam), made of layers of dimensional lumber (lumber that is cut to standardized width and depth) bonded together with durable, moisture-resistant glue. These days the most frequently used mass timber product in construction is cross-laminated timber (CLT). This product, which looks like a giant butcher block, is made using dimensional lumber, cross thatched with glue on a giant press and placed under extreme pressure. CLT panels can be as large as 12 x 40’ and 12 inches thick. They are structurally stronger and lighter than both steel and concrete and have been widely adopted in Europe, East Asia and Japan. Other variations include Dowel Laminated Timber (DLT) which uses wooden dowels to connect boards together, and Nail Laminated Timber (NLT) where the boards are nailed together.
The biggest drawback of these technologies is that they use a lot of wood, making them susceptible to market fluctuations. Just recently, prices soared by almost 200%.
New mass timber products are in development and Scott Ehlert’s cassette system is one of them. Scott, co-founder of Fabric Workshop, is designing a proprietary hollow core mass timber plate column and wall system that uses 50 percent less wood fibre and will cost 10 – 35 percent less overall than a CLT structure. The box-like panels consist of two outer layers with a hollow core and an internal membrane to retain structural integrity. The advantage of the cavity is that what would normally be exposed in a CLT building – mechanical, electrical, and plumbing systems – can be integrated right into the panels. Insulation, acoustic, seismic and fire safety materials can also be added.
Fabric Workshop is based in California and while it hopes its product will help address the state’s housing affordability challenges, the company also sees an opportunity to impact California’s wildfire crisis. In 2020 the state’s fire season was 75 days longer than just 20 years before. Removing excess unnatural growth out of forests would help to reduce the severity of those fires. Right now, those small and medium diameter trees have no value but Fabric Workshop wants to create a market demand by using them in advanced cassette-based plate systems. Instead of dimensional lumber, they are focusing on another sub-product of mass timber known as laminated veneer lumber, or mass plywood, which is made from peeled timber sheets glued together.
Scott hopes that forestry industries, which have reduced by 70 percent in the last 45 years, will return to California with a much greater technological, environmental, and ecological focus. Timber is an environmentally friendly building product which offsets the carbon and environmental impacts of concrete and steel. Sourcing it locally and preventing wildfires are the icing on the cake.
Image from PxHere