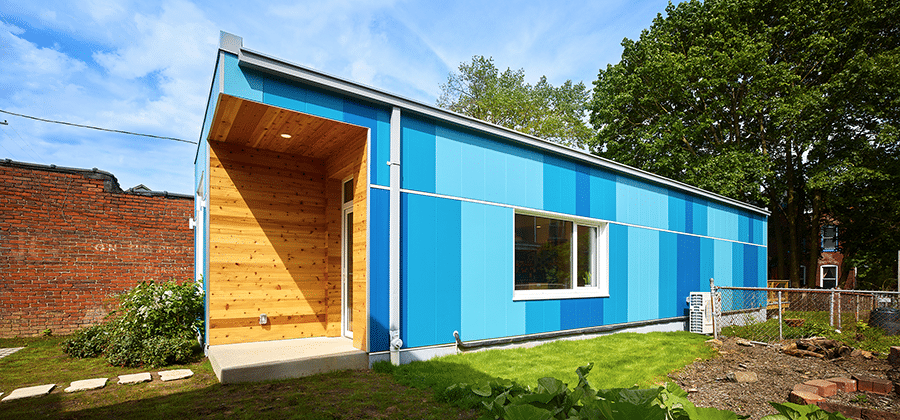
As builders, architects, urban planners all look for innovative ways to create both affordable and sustainable housing, some new homeowners have been looking to the efficiencies of modular construction as one potential solution. While pre-fab (for pre-fabrication) is a general term for building components that are created in a factory to be assembled on site, modular construction refers to pre-finished volumes, about 70 percent complete. In other words, entire rooms or floors – modules that can be set down on a property virtually ready to go except for hookups and exterior finish work.
One such example is Module, based in Pittsburgh. Module was co-founded by a trio of young entrepreneurs who were inspired by the idea that everyone should have access to good design. But as opposed to the typical design-build company that gives clients the options of picking from only a few template plans, Module’s team offers turnkey design-build-develop services. They do not build the homes but work with a third-party manufacturer and a third-party contractor, managing the whole process for clients from start to finish, from design to permitting to construction.
Why build this way?
Basic modular, or even pre-fab, construction offers a variety of benefits for the homebuyer. On the one hand, as opposed to designing a home from scratch, which is time-consuming and adds additional cost, a developer or builder can offer a new homebuyer templates based on their needs and budget.
There is also the benefit of a large reduction in construction time, and when done at large scale, construction costs. Modular projects also offer high-quality, factory-based construction, often using eco-friendly materials and energy-efficient, customized designs, all with rapid on-site assembly. Already familiar in countries like Japan, this way of building housing is starting to become popular in the U.S., and most exciting, offers innovative methods for providing affordable and sustainable housing on a large scale.
One reason for the trend towards pre-fab and modular construction is a shortage of skilled labor in many housing markets. Another is a supply shortage in boom markets, where existing developers cannot build things fast enough. In both cases, components of a building can be constructed anywhere and shipped to the site. This has long been the case, for example, with pre-fabricated roof trusses one often sees being trucked along on the highways.
Module
Brian Gaudio, the CEO of Module, created his company differently. He describes the vision of Module as more of a tech startup company than a design firm, offering their product first and foremost as a service, or process that you can literally order online. “We’re trying to redesign the customer experience,” he says, “and redesign homeownership from the ground up.”
First, Module works to understand the clients’ current needs, learning what they want in a home – everything from space and light, to aesthetics and utility. Second, for clients who already own land, Module evaluates the site location and determines what’s possible based on topography and local zoning rules. If a client needs to purchase a lot, Module offers a curated selection of available lots they know will work with their designs.
Third, the team works to design the client’s home and create a budget. Fourth, Module handles all of the permitting and manages every aspect of the building process. Because they partner with manufacturers and contractors, he says, “we don’t own those parts of the supply chain. But what we do own is the customer experience.”
Finally, and perhaps most importantly, Module plans to grow with their clients, offering the flexibility to add more space as needed with additions that are made to grow a home to order.
The future
Modular construction offers exciting solutions for both affordable and sustainable housing. There are a number of innovative options available now, and while some companies offer services nationwide, it’s also worth exploring local companies to learn about options in your area.
Listen to our interview with Module founder, Brian Gaudio, to learn more about how Module is bringing their unique modular process to the Pittsburgh area.
Image courtesy of Module Housing