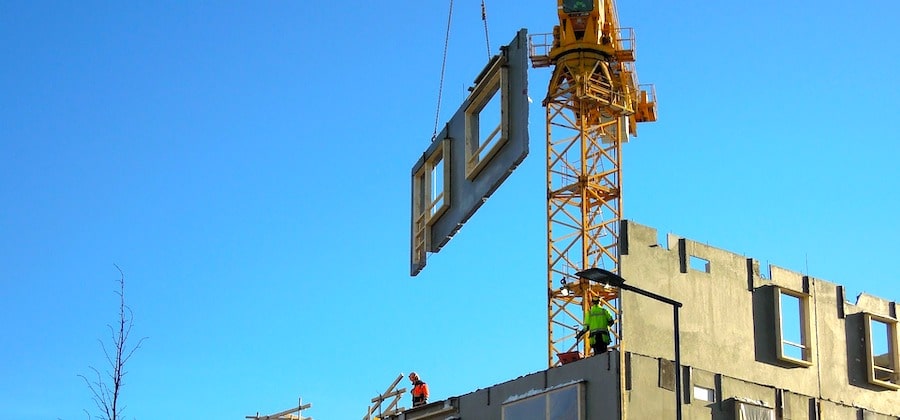
The residential and commercial building industry has changed radically in the last few decades, following the pattern of many other vital sectors of the US economy. Two of the developments that the industry has been focused on, which happen to be interlinked, are prefabrication and offsite construction. Coupled with this, vertical integration is a focus of many companies as they seek ever more technologically advanced efficiencies. Compared to ten years ago, building projects today require less labor and have a faster construction cycle. Both of these factors have been driving down construction and labor costs for large-scale builders. The question is will prefab construction upturn the industry further and change how we build in the future? Maybe.
Prefab and offsite construction
Prefab buildings are not new. As early as 1908 Sears Catalog Homes started being sold through the Sears catalog with a reported 40,000 sold in North America between 1908 and 1940. Although the catalog home trend waxed and waned, much ado was made regarding modular construction. But at that time modular construction resulted in an entire generation of utilitarian and bland prefabricated buildings that were far more function than form. Now the offsite construction industry has moved beyond a purely functional role and offers pre-made, cost-effective and attractive structures for every purpose, from single-family homes to skyscrapers and everything in between.
Some larger companies are taking up prefab construction initiatives, such as the hotel-giant Marriott, which is undertaking six projects nationwide. Rehab construction specialists like Clark Pacific and Guerdon Modular buildings are reporting significant upticks in prefab orders across the country. At the same time building contractors are becoming more familiar and comfortable with the modular construction process, and designers are recognizing that prefab buildings can allow for significant flexibility, while not constraining innovation or imagination.
Benefits offered by prefab
A combination of lowered labor, building and material costs along with the ability to design a prefab structure from scratch, makes this industry sector especially enticing for both commercial and residential buildings that need to be replicated. Some examples of potential growth areas include fast-food buildings, hotels, coffee shops, and other spaces that follow a standard design and use pattern.
Labor costs
One of the most significant prefab drivers is not just the cost savings in on-site building labor. It’s the ability to build quickly in an industry in which there are simply not enough skilled workers available. For the last two years the multifamily and affordable housing sector has been hit particularly hard by a shortage of workers. This in turn drives up project costs and can cause building cost overruns or expensive delays in the completion of projects. Offsite manufacturing has the potential to not only solve these problems, but to reduce project schedules as well.
Controlled manufacturing environments
There is a pretty stark difference between the average manufacturing facility and most building sites when it comes to cleanliness and control of the site. Construction sites must be prepared for exposure to the elements, security and safety risks posed by trespassers, unwanted intrusion by animals or birds and a whole host of other problems. These prevent building sites from being ideal manufacturing facilities. Offsite construction avoids all of these problems as the building process is completed inside a clean and controlled warehouse facility.
Opportunities for collaboration
While not so long-ago architects, builders and other real estate professionals turned their collective noses up at the mention of a prefab building, today there is plenty of dialogue between all of these sectors – they want to be involved in prefab building design and manufacturing. Many designers are embracing prefab as the way of the future.
_
In an era of shrinking margins and growing costs in the development and construction space, prefab makes sense. It can be applied on scale, with no limitations on size or scope. Prefab skyscrapers are already being erected in many Chinese cities, with structures as tall as 57 stories high being built in less than 20 days. While the United States has lagged behind many Asian and European cities with their embrace of modular construction, astute developers and builders are beginning to leverage this new(ish) technology to reduce costs, improve build times, and introduce new levels of efficiency to operations.
Image by AI Leino from Pixabay